A 14-Step Inspection Checklist For Pressure Washer Maintenance
Published:
6/23/2021
A pressure washer is a crucial tool for the operations of general contractors in industries such as transport or agriculture. A potential breakdown could cause a delay in your cleaning schedule, which effectively reduces your productivity and profitability.
It's crucial to plan for periodic maintenance as a measure to avoid frequent breakdown or stalling. Here is a 14-step inspection checklist for pressure washer maintenance.
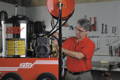
Pressure washer maintenance - before use
1. Water, Fuel, and Oil Levels
Oil: Use a dipstick to check oil levels; if low, add some oil to reach the calibrated level. Check its color for milkiness or dark coloration. These are indicators of a need to change the oil. If you haven't changed the oil recently, it's important to consider changing it.
Water: Ensure the water reservoir has clean and adequate water levels. Check and remove any debris at the inlet valve; if you're using a floating tank, fill it up to confirm the self-shutting function.
Fuel: Always fill up the fuel reservoir to mitigate downtime associated with low fuel midway through an operation.
2. High-Pressure Hose and Nozzle
Check the high-pressure hose for possible cuts, breakages, or weak lines. If you notice a defective hose, use the manufacturer's manual to acquire a suitable replacement. It's advisable to keep an extra hose on standby to avoid downtime.
Examine the nozzle for possible damage or clogging. A damaged nozzle reduces the pressure and your productivity. You can start the pressure washer with low pressure and without the nozzle to unclog any stuck debris.
3. Drive Belt
Turn off the machine to check the drive belt tension and its wear and tear. Check the belt tension by applying force at the top and midway on the pulley system. The ideal deflection (Belt length * 0.016) should be between ¼ — ½. If it's greater than that, consider tightening the belt.
4. Scale Deposits
The formation of scale deposits is a common problem in areas that have hard water. It affects pipe heads, valves, and heat exchange systems which makes the coil overheat. Scaling creates deposits of impurities such as calcium, chloride, and silicate in the coils. These impurities restrict the normal flow of liquid and pressure, thereby reducing the effectiveness of your pressure washer. You can disassemble the coil system and descale using white vinegar or any available descaling product.
5. Power Cord
A defective power cord can expose an operator to electric shock or a possible fire incident. As such, it's crucial to check the physical condition before you start operating the machine. Check for any potential damage including cuts, exposed wires, or a defective part. The fundamental consideration is safety, so it's ill-advised to operate a pressure washer with defective cords or signs that pose a danger.
6. Surround Area
You should not operate a pressure washer on untested grounds — use a multimeter to assess continuity. Alternatively, ensure the electric cords have appropriate ground fault interrupters. In addition, a circuit breaker marked 20 amps, or more is ideal for managing intermittent power effectively.
pressure washer maintenance - during use
7. Fluid Leaks
A pressure washer sometimes leaks water leading to milky oil, messy working areas, and eventual stalling. Some common sources of leaks include an inlet, pump, piston seal, or thermal release valve.
You can check the outlet seal for any leaks or cracked hoses. Replace with a new O-ring or repair the pipe to mitigate potential damage to the equipment. Check the float tank for possible leaks by filling it with water to identify bleeding points.
8. Condition of System Pressure
Turn on the machine to check whether the pressure washer operates within 5-10% of the normal pressure gauge. Use the equipment pressure gauge to assess whether the equipment is within normal range.
Disparities in air pressure can result from either a defective nozzle, malfunctioning unloader, or air leaks in the system. Open and close the trigger several times to release any pressure clogs. Alternatively, check for any nozzle wear, which could be the cause of pressure disparities.
9. Chemical/Detergent Delivery
Debris in the chemical delivery system affects the cleaning procedure by inhibiting the regular mixing of detergents. It can be caused by a defect in the valve or the downstream injection system. You can solve that by introducing a chemical filter or changing the valve to perfect the filtration system.
10. Trigger Gun
A defective trigger gun can cause the pressure washer to start or stop without the input of an operator. Check for damage at the inlet, outlet, nozzle, or valve. If the gun is leaking at the nozzle, you'll need to replace the valve to improve the effectiveness of the air unloader. Remove the gun for repair if it sticks persistently — ideally, it should operate smoothly with minimal resistance.
11. Burner Operation
Install a filter in the burner fuel liner that you should check and drain daily. You should also replace the filter every two months. Ensure fuel in the burner tank is always full to minimize condensation.
pressure washer maintenance - after use
12. Check Heat Exchanger for Sooting
Soot results from a build-up of carbon deposits, which eventually make the heat exchanger malfunction. Disassemble the coils and remove the soot to avoid overheating during an operation.
13. Check Chemical Inventory
After completing the operation, wash the detergent/chemical compartment by rinsing it in running water for 2 minutes. You can also refill it to get ready for the next cleaning schedule.
14. Verify Cool Down Phase
It's crucial that the pressure washer cools down before storage or commencing another cleaning exercise. Allow 10-20 minutes of cool-down time, which will allow oil, heat exchange, and water to settle down for optimal performance.
let us help you maintain your pressure washer
Routine maintenance of your pressure washer is necessary to keep your equipment running and prevent constant breakdown. As such, the above pressure washer inspection checklist for thorough maintenance is a great resource for your continuous workflow.
Nonetheless, executing technical maintenance — like descaling or sealing fluid leaks — requires the services of a professional company like Nortex Sales and Service in Dallas. We're highly experienced in the maintenance and repair of pressure washers, specifically for professionals in the oil, transport, gas, and waste management industries. Call us today to schedule a maintenance trip or repair.
To find out more about pressure washer maintenance, check out our complete pressure washer maintenance handbook here.
Share this Article ↓